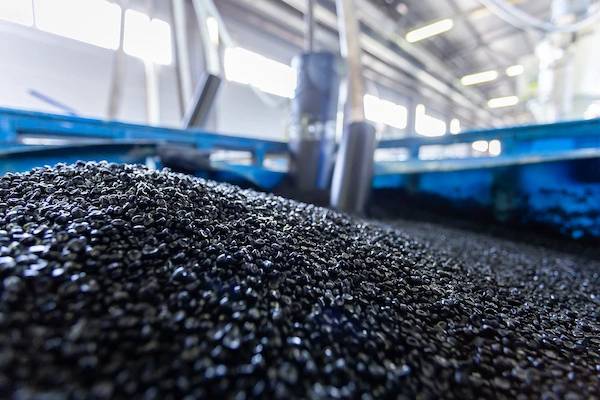
It might not sound like the most exciting subject, but the creation of polyethylene and thereafter polythene is actually really interesting. Read on to find out why.
From its humble beginnings as ethylene gas to its transformation into a multitude of everyday products, let’s dive into the world of polythene production.
The Journey of Polythene
Sourcing Ethylene
Polyethylene starts its journey as ethylene gas, a colourless hydrocarbon compound. Ethylene is primarily derived from natural gas or crude oil through a process called cracking.
Cracking involves the breaking down of complex hydrocarbon molecules into simpler components, including ethylene.
This crucial step sets the stage for the creation of polyethylene.
Polymerization Process
The next step in polyethylene production is polymerization. Ethylene gas is subjected to high temperatures and pressures within a specialized reactor.
Catalysts, such as titanium or chromium compounds, are introduced to facilitate the polymerization process.
These catalysts help bind the ethylene molecules together, transforming them into long chains known as polymers.
Varied Polymerization Techniques
Polyethylene can be produced using different polymerization techniques, each resulting in unique properties. The two primary methods are high-density polyethylene (HDPE) and low-density polyethylene (LDPE).
HDPE is created by utilising high pressures, leading to a dense and rigid polymer structure. On the other hand, LDPE is produced under lower pressures, resulting in a more flexible and malleable polymer.
Processing and Shaping
Once the polymerization is complete, the polyethylene is typically in the form of pellets or beads. These pellets undergo various processing techniques to mold them into the desired shapes.
Extrusion, injection molding, and blow molding are commonly employed methods in shaping polyethylene. Extrusion involves melting the pellets and forcing the molten polymer through a die to create continuous shapes like pipes or sheets. Injection molding injects the molten polyethylene into a mold cavity, forming intricate shapes like bottles or containers. Blow molding uses air pressure to expand the molten polymer inside a mold, producing hollow objects like bottles or tanks.
Adding Additives
During the processing stage, additives may be incorporated to enhance specific properties of the polyethylene. These additives can provide increased flexibility, UV resistance, colouration, or other desired characteristics. Common additives include antioxidants, UV stabilisers, colourants, and fillers.
Recycling and Sustainability
Polyethylene has the advantage of being recyclable. Recycling processes involve collecting used polyethylene products, cleaning and sorting them based on type, and melting them down to form new polyethylene pellets. Recycling not only reduces waste but also helps conserve valuable resources and energy, making it an important aspect of sustainable production.
Polyethylene, or polythene, is a remarkable polymer that plays an integral role in our daily lives. Through the process of sourcing ethylene, polymerization, shaping, and incorporating additives, polyethylene transforms from a gas into a versatile material used in countless applications. By understanding the intricate journey of polyethylene production, we can gain a deeper appreciation for this widely utilised and adaptable polymer.For more information about the range of polythene products we can offer, get in touch today.